Tools Used in Custom Sheet Metal Fabrication
Metal fabrication is the complex process by which raw metals are transformed into an array of products used on the ground floors of hospitals to the highest of airplanes. The three stages of sheet metal fabrication use a variety of sheet metal fabrication tools, depending on the specifications of any custom order. Custom sheet metal fabrication can impact the tools used during structuring, chopping, forming, and finishing.
Structuring the Job
The first stage of sheet metal fabrication is in which the general structure of the product is developed. Imagine pressing out the dough while cooking into a flat shape so that you can turn that dough into a usable product. Instead of dough, sheet metal fabricators are working with metals. And instead of cookies, they are making metal fixtures that could be saving your life while in the hospital. The sheet metal fabrication tool for structuring is primarily a forming press (or more commonly just called a press). Custom sheet metal fabrication can use a variety of presses that are generally categorized along with two characteristics: mechanism and function.
The mechanism of a press is the source of movement that allows this sheet metal fabrication tool to complete its task. According to the Library of Manufacturing, there are three distinct mechanisms on which a press operator relies: hydraulic, mechanical, or pneumatic. A hydraulic press is one in which pressures (traditionally created by water or some other benign liquid) inside the press system provide the force necessary for the job. A mechanical press relies on a motor system (either man-powered or through the burning of fuel or electricity). A pneumatic press is powered by pressurized gases.
The forming press can also be categorized by the function, or type of forming, that the press completes: forging, braking, stamping, and punching. Forging presses are those which shape and distribute weight across a sheet metal much like a blacksmith would hammer out metal into the rough shape of a product. Press braking is the tool responsible for producing predetermined bends during custom sheet metal fabrication. Stamping is the process of using a press with a mold to create specific shapes during sheet metal fabrication. Punching is the forming press responsible for producing the holes necessary during sheet metal fabrication such as those through which a screw will adhere to two metal structures. A single product can rely on multiple forming presses during sheet metal fabrication.
Chopping the Job
After the general shape is achieved with the sheet metal fabrication tools of pressing, the task of cutting can begin to get the sheet metal into a more desired size. The cutting process of sheet metal fabrication can be accomplished through multiple methods, including sawing, torching, or numerical control cutting. Each of these methods has multiple possible tools that can be selected depending on the particular specifications of a custom sheet metal fabrication job.
The traditional chopping methods include sawing, shearing, or chiseling. Sawing is the use of a blade, chain, or wire to make cuts in metal. Sheet metal fabrication tools used for sawing can include: hacksaw, chop saw, jigsaw, and band saw. Shearing is the use of a sheet metal fabrication tool that functions as a pair of scissors, including alligator shear, bench shear, guillotine, power shears, throat-less shears, and tin snips. Chiseling is a sheet metal fabrication tool that comes in a variety of shapes with the designed goal of pushing through sheet metal. For metalworking, chisels are typically designed to work with either cold or hot metals. Across all of these chopping sheets, metal fabrication tools are variations of the power source of these tools (either manual or powered).
Other Forms of Chopping
Torching is a form of chopping which relies on the principles of welding. Torching consists of two major forms of hand-held torches: oxy-fueled and plasma torches. Oxy-fueled torches combine oxygen with fuel gas to maintain heat that cuts through metal by melting it. Plasma torches are a similar product but instead of relying on the relationship between oxygen and particular gases, this cutting torch relies on the heat produced by turning a gas into a plasma (a state of matter comparable to the sun!).
Numerical control cutting is a state-of-the-art form of cutting that relies on computer-programmed cutting technologies for precise and accurate custom sheet metal fabrication. The numerical control cutting can be a modified version of other forms of cutting, such as torches, or can incorporate different cutting technologies, such as lasers, water jets, or mill bits. In fact, most sheet metal fabrication tools that rely on numerical control cutting incorporate multiple forms of cutting (e.g., saws, lasers, chisels, and torches among others) into a single cell or unit.
Forming the Job
Once the general shape and size of a product are constructed, the sheet metal product is often put into a more finely tuned shaping process. A product being constructed through custom sheet metal fabrication will often return to a more precise forming press in which additional braking, punching, or punching can be accomplished. Additionally, refinement forming tools, such as planishing or power hammers, are used for more precise forming such as beading, doming, edging, and shrinking.
Sheet metal fabrication tools of assembly are also used during forming and include riveting, welding, and bonding adhesives. Depending on the specifications of a job for custom sheet metal fabrication, any number of tools can be used and are too numerous to list. In fact, some tools are created just for the purposes of assembly of sheet metal fabrication.
Finishing the Job
After shaping, cutting, and forming, a sheet metal fabrication product is finished. The main focus of finishing is giving the sheet metal product a smooth finish and nice look. The first tool is designed to smooth the finish of the sheet metal: an abrasive blaster. Pressurized air or fluid propels a variety of abrasives against the surface of the metal. Those abrasive blasters can include bead blasting, soda blasting, and sandblasting. A bead blaster uses fine glass beads to clear debris. Sodablasting is the release of sodium bicarbonate through pressurized air to smooth a metal surface. Sandblasting sends grains of sand against a sheet metal fabrication product to smoothen out the surface.
The particular type of abrasive blaster will be determined by the metal and desired finish of the product. A custom sheet metal fabrication specialist will be particularly useful in determining the appropriate blaster for a specific job. After the sheet metal is smooth, the finished product can be painted to match whatever desired aesthetic is desired. The numerous sheet metal fabrication tools make the complex process of sheet metal fabrication feasible and successful. These various tools have allowed sheet metal to be the key ingredient in every possible domain of human life and interest, from airlines to zoos.
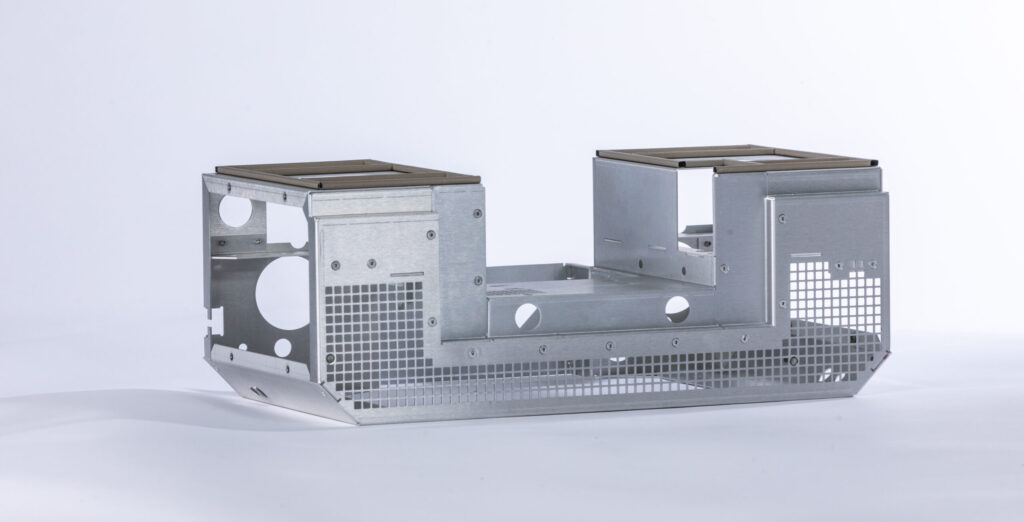